WHAT IS AGITATED scraper THIN FILM EVAPORATOR ?
The AGITATED scraper THIN FILM EVAPORATOR is a kind of forced film formation by rotating scraper. It is can be falling film evaporation in the vacuum condition through the rotating scraper forced film formation. Agitated thin film evaporator is a new type of high efficiency evaporator.
How does an agitated film evaporator work?
Agitated thin film evaporator working principle as follows:
The scraper agitated film evaporator is a kind of high efficiency evaporation & distillation Machine. That’s make sure of high-speed rotating liquid distribution into uniform thin film evaporation and distillation of a highly efficient evaporation. Distillation equipment. can also be used for deodorization. deaeration reaction. heating. cooling unit operation.etc. This equipment adopts the centrifugal rotor of the sliding groove. It is the foreign latest evaporator structure. Under the condition of the traffic is very small. Also can form a thin film. On the inner wall of the cylinder in evaporation processing . The adhered on the surface of the liquid in the warp can be scraper quickly removed. And compared to fixed clearance scraper evaporator. evaporation can be increased 40-69%.
TECH DRAWING OF THE AGITATED SCRAPER THIN FILM EVAPORATOR AS FOLLOWS:
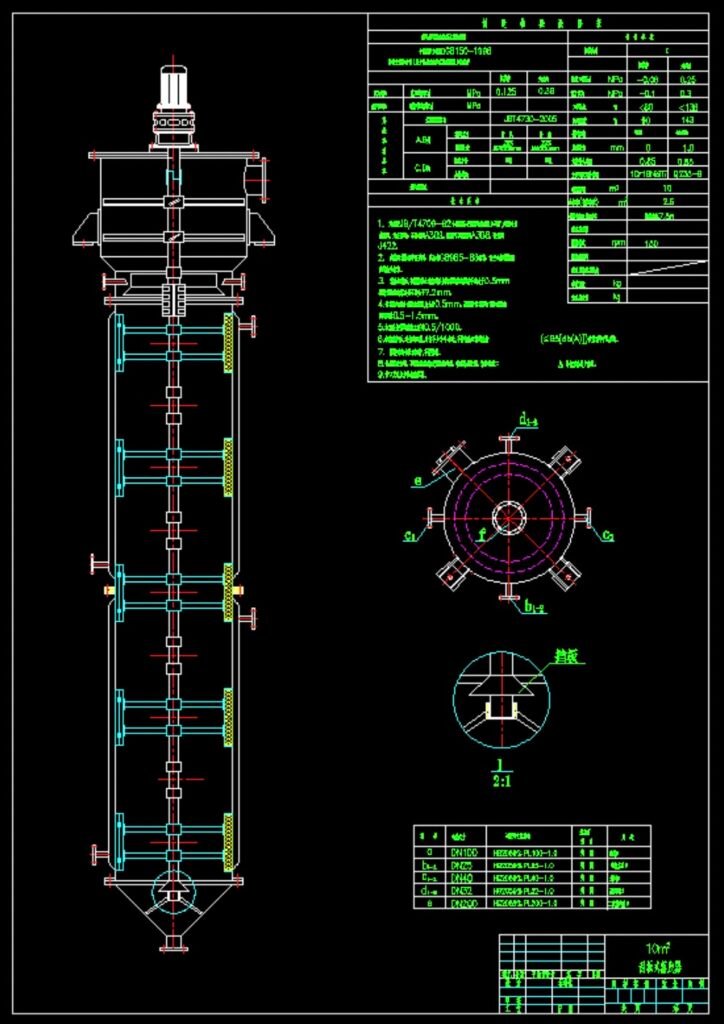
Main feature:
-High heat transfer coefficient.high evaporation capacity.The evaporation intensity can reach 200 kg/m2.hr, high thermal efficiency.
1.The material of the AGITATED scraper THIN FILM EVAPORATOR heating time is short. About 5 to 10 seconds. Wok in in a vacuum conditions which is more favorable for heat-sensitive materials. Keep all kinds of ingredients without decomposition to ensure the products quality.
– Adapt to the wide range of viscosity changes. High and low viscosity materials can be treated, and the material viscosity can be up to 100,000 CMP (CP)
– Low pressure drop is advantage of Agitated thin film evaporator.
-A certain pressure difference is required to deliver the evaporated material from the heating surface to specified condenser in the state of steam. In a typical evaporator. this pressure drop (inhalp) is generally high and sometimes unacceptably high. However. The gas in the film evaporator has a greater ability to cross space. And the pressure in the evaporator can be regarded as almost equal to the pressure in the condenser. The pressure drop loss is small.
– Change the rotation direction of the scraper groove and adjust the operation time of the material in the evaporator.
– The inner wall of the cylinder of the evaporation section has been carefully boring and polished. The surface is not easy to cause coking and scaling.
– Easy to operate and easy to adjust the product index. Under closed conditions, continuous production can be carried out automatically.
– Small floor space, simple structure, convenient maintenance and easy cleaning
AGITATED THIN FILM EVAPORATOR FEATURES:
Thin film evaporators have the following unique advantages. Which are unmatched by conventional film evaporators:
1. Extremely small pressure loss In the rotary scraper film evaporator. The material “flow” and the secondary steam “flow” are two independent “channels”. The material is descending along the inner wall of the evaporation cylinder (forced film formation). The secondary vapor evaporated from the evaporation surface leaves the evaporator almost unimpeded from the space in the center of the cylinder. So the pressure loss (or resistance drop) is minimal. For this
2. It can realize operation under real vacuum conditions
Because the resistance of the secondary steam from the evaporation surface to the condenser is extremely small. The evaporation surface of the inner wall of the entire evaporation cylinder can maintain a high vacuum degree (up to -750mmHg or more). Which is almost equal to the vacuum degree of the vacuum system outlet. Due to the increase in the vacuum level, the boiling point of the treated material is effectively reduced.
3. High heat transfer coefficient, high evaporation strength
The decrease of the boiling point of the material increases the temperature difference with the hot medium. Liquid film in turbulent flow state reduces thermal resistance. Similarly, inhibiting the coking and scaling of materials on the wall also improves the heat transfer coefficient of the evaporation cylinder wall. The total heat transfer coefficient of the high-efficiency rotary film evaporator can be as high as 8000KJ/h·㎡·°C. So its evaporation intensity is very high.
4. Low temperature evaporation
Since the high vacuum level can be maintained in the evaporation cylinder. The boiling point of the treated material is greatly reduced. So it is particularly suitable for low-temperature evaporation of heat-sensitive materials.
5. Short overcurrent time
The overflow time of the material in the evaporator is very short. About 10 seconds of soil. No coking. No scaling. For the commonly used movable scraper. The end face of the scraped animal material has a groove with diversion. And its bevel angle is usually 45°. Changing the angle of the bevel can change the overflow time of the material. And the material is spirally down and leaves the evaporation section under the scraping of the scraper. Shorten the overflow time and effectively prevent the product from decomposing, polymerizing or deteriorating during the evaporation process.
6. Low-grade steam can be used
Steam is a commonly used hot medium. Due to the reduction of the boiling point of the material. Under the condition of ensuring the same Δt. The temperature of the heating medium can be reduced. And the use of low-grade steam is conducive to the comprehensive utilization of energy. It is especially suitable as a final evaporator for multi-effect evaporation.
7. Strong adaptability and easy operation
The unique structure design makes the product can handle some high-viscosity. Particle-containing. heat-sensitive and crystallization materials that are not easy to be handled by conventional evaporators.
The rotary film evaporator has great operating flexibility. stable operating conditions. small maintenance workload and convenient maintenance.
Form factor and actual device size may vary slightly for reference.
1. Jacket pressure. conventional design according to 0.4Mpa steam. Can also be designed according to user requirements. When using heat transfer oil. can also be designed separately.
2. Evaporation cylinder vacuum. Conventional -0.09Mpa (about -680mmHg). can also reach -0.095Mpa (about -720mmHg) and -0.0986Mpa (about -750mmHg) according to user requirements.
3. Main cylinder (part in contact with the material) and jacket material. According to the needs of users and actual needs. Carbon steel.SUS304.316L. 316Ti.310S or titanium. nickel. etc. can be used .
Structure of the agitated scraper thin film evaporator
1.Motor and Reducer of the agitated film evaporator
It’s the drive device of the rotor rotation. The rotation speed of the rotor is depends on the type of the scraper. The viscosity of the material and the inner diameter of the evaporation cylinder. Selecting the appropriate linear speed of the scraper is one of the important parameters to ensure the stable and reliable operation of the evaporator and satisfactory evaporation effect.
2.The separation of the cylinder
-Material enters the evaporator tangentially from the inlet located at the lower end of the separation cylinder. And is continuously and evenly distributed on the inner wall of the evaporation cylinder by the distributor installed in the separation cylinder. And the secondary steam evaporated from the evaporation cylinder rises to the separation cylinder. And the gas-liquid separator installed separates the droplets or foam that the secondary steam may carry. And the secondary steam leads out of the evaporator from the outlet at the upper end.
-The rational design of the separation cylinder based on the calculation of resistance in the evaporator is one of the key factors to avoid “short circuit” of the material. (The so-called “short circuit” means that the material has just entered the evaporator and has not completed the evaporation process. That is. it leaves the evaporator from the secondary steam outlet.)
3.The spreader of AGITATED SCRAPER THIN FILM EVAPORATOR
spreader of the agitated thin film evaporator is installed on the rotor. Reasonable design. So that the material entering the evaporator from the tangent direction is continuously and evenly spread on the evaporation surface through the rotating distributor.
4.The gas-liquid separator of AGITATED THIN FILM EVAPORATOR
The gas-liquid separator rotary vane gas-liquid separator is installed above the separation cylinder. Which captures the droplets or foam . That’s may be carried by the rising secondary steam and makes it fall back to the evaporation surface.
5.The evaporation cylinder of AGITATED scraper THIN FILM EVAPORATOR
-The evaporation cylinder is also known as the heating cylinder. It is an evaporation surface where the material forced to form a film by the rotating scraper and the heating medium in the jacket are heat exchanged. The inner diameter and length of the evaporation cylinder are determined by the evaporation area and the appropriate length-to-diameter ratio.
-The inner wall of the heating cylinder is processed and polished by a special machine tool. And the flange connection surface at both ends is processed at one time to ensure the overall centeredness of the equipment. After polishing (if necessary. mirror polishing). The inner wall of the barrel is smooth and bright. and it is not easy to stick and scale. Which effectively ensures the high heat transfer coefficient of the equipment.
5.1.If the heating medium is steam. the heating cylinder generally adopts the jacket type.
5.2.If the heating medium is heat transfer oil or high-pressure steam. The heating cylinder generally adopts the type of half pipe.
6.The rotor of AGITATED scraper THIN FILM EVAPORATOR
The rotor installed in the evaporator cylinder is composed of a rotating shaft and a rotating frame. The rotor is driven by a motor and reducer, and drives the scraper to make a circular motion. The rotating frame is processed by stainless steel precision castings. So that its strength. geometric size and stability are effectively guaranteed.
7. Scraper Type:
-Due to the movement of the scraper. The material is continuously scraped into a film on the evaporation surface to achieve the effect of film evaporation.
-According to the viscosity and other characteristics of the material.there are the following three scraper types of the agitated scraper thin film evaporator to choose from.
Scraper type 1
(1) Sliding scraper Sliding scraper is one of the most basic and common forms of scraping. The scraper is installed in the four scraper guide grooves of the rotor. And is thrown radially to the wall of the evaporation cylinder due to the centrifugal force of the rotor rotation. And at the same time makes a circular motion with the rotor. This scraping of the scraper makes the material in a film-like turbulent state on the evaporation wall. Which greatly improves the heat transfer coefficient. And at the same time. this continuous scraping effectively inhibits the overheating.dry wall and scaling of the material. Generally. The scraper is made of filled PTFE. Which is suitable for a working temperature below 150 °C. When the evaporation temperature is higher than 150°C. Carbon fiber is used. The end face of the scraper is machined with an angled liquid transfer tank.
Scraper type 2
(2) Fixed scraper fixed scraper are made of metal material. It is rigidly connected to the rotor. The length of the scraper is the same as the evaporation cylinder. The gap between the rotating scraper and the inner wall of the evaporation cylinder is only 1-2mm. Requiring high processing and installation accuracy. It is suitable for evaporation concentration. desolubilization or purification of ultra-high viscosity and foam-prone materials.
Scraper type 3
(3) Hinge scraper This scraper is suitable for materials that are easy to scale on the heating surface. And the scraper usually uses metal parts. And the scraper is installed on the rotating frame by means of movable hinges. When the rotor rotates. Due to the action of centrifugal force. The scraper is tightly pressed on the inner wall of the evaporation cylinder. And slides on the wall at an angle (with the wall) to scrape the material into a film and prevent the wall from scaling.
8.The bottom seal head
The W-shaped bottom seal head is separately designed with the bottom sealing head. And is equipped with high-temperature self-lubricating bearings. Which is not only convenient for the discharge of materials. But also convenient for the maintenance and repair of the bottom bearing. Above is the structure of our AGITATED scraper THIN FILM EVAPORATOR introduction .
Agitated thin film evaporator scope of use :
1.Chemical Industry : The agitated thin film evaporator is widely used in petroleum and chemical industry .
2.Food industry:The agitated film evaporator equipment used to separate and concentrate food. for example :milk.Juice.Tea etc.
3.Petrochemical industry:The agitated thin film evaporator equipment used to separate and purify all kinds of petroleum products.
4.Environmental :The agitated thin film evaporator used to separate and concentrate wastewater.Dirt etc.
5.Polymer industry:agitated thin film evaporator used for manufacture of paints and high quality polymer.
Agitated thin film evaporator equipment.
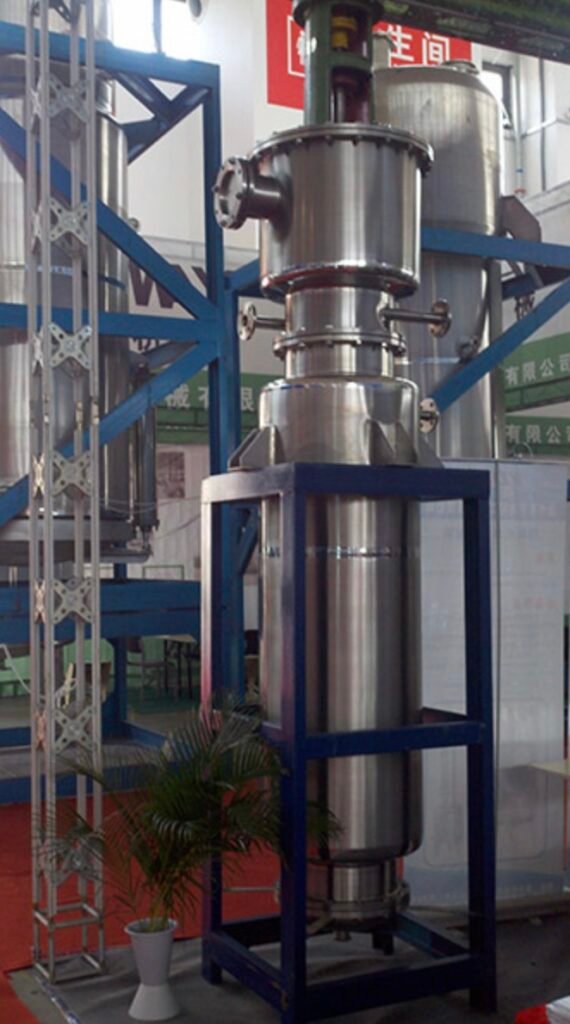
AGITATED SCRAPER THIN FILM EVAPORATOR Technical Data:
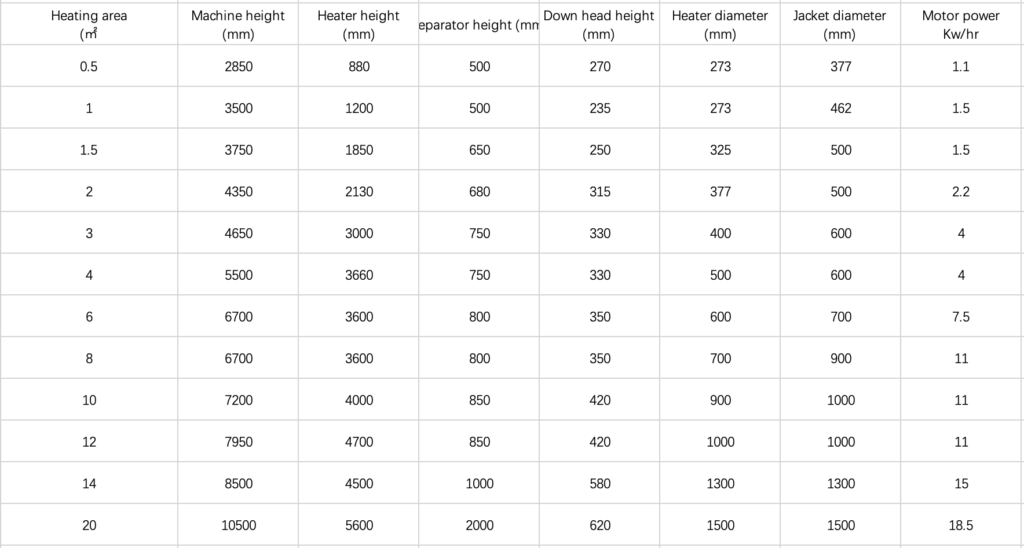